Understanding Die Casting: A Comprehensive Guide to Die Casting Die
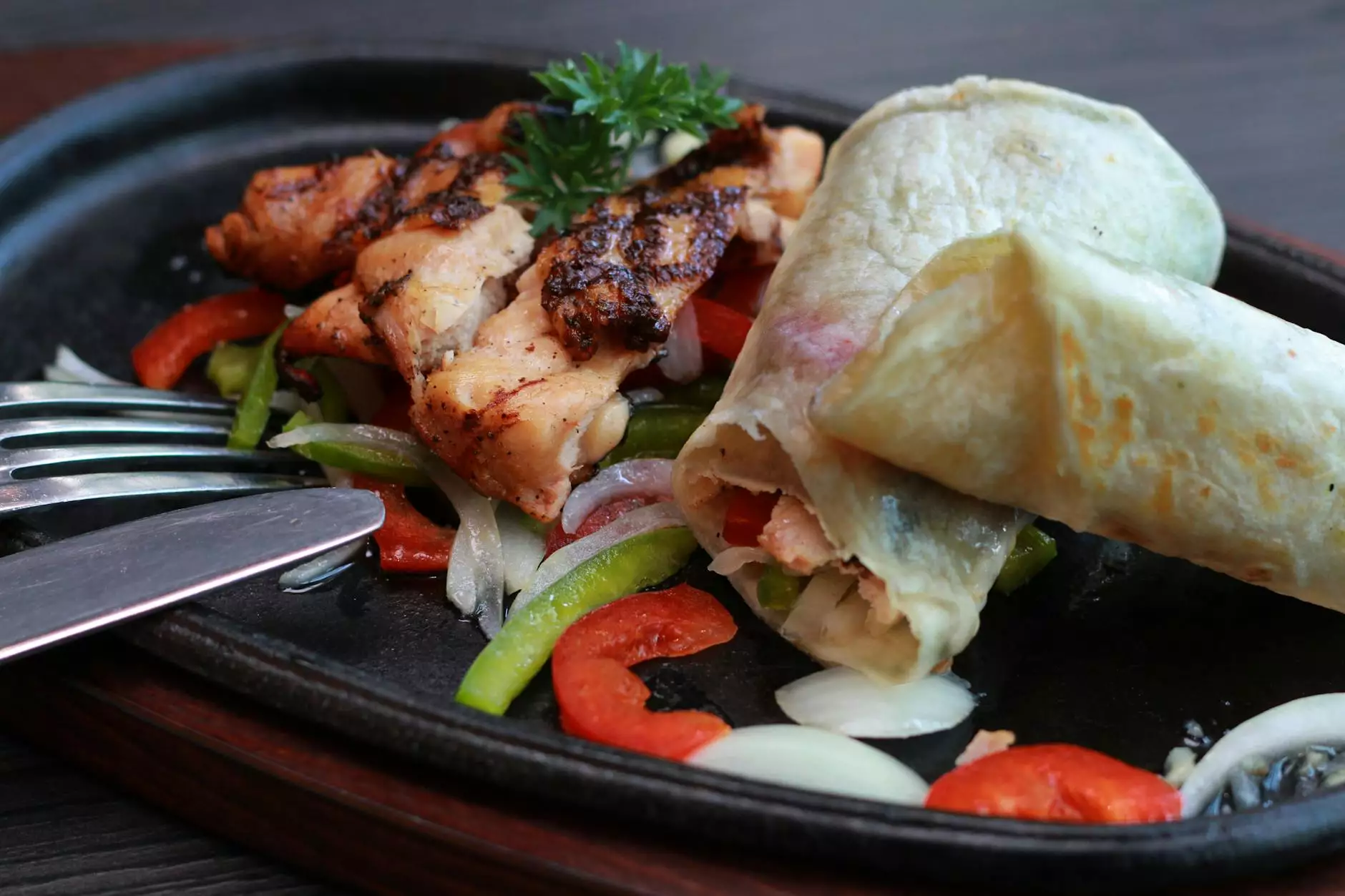
Die casting is a vital manufacturing process that allows for the production of complex metal components efficiently and cost-effectively. At the heart of this process is the die casting die, a critical tool that shapes the molten metal as it is injected into a mold. This article delves into the intricacies of the die casting process and the paramount role that the die casting die plays in the world of metal fabrication.
What is Die Casting?
Die casting is a metal casting process that involves forcing molten metal under high pressure into a mold cavity. This process is distinctive when compared to other forms of casting due to its ability to produce parts with high dimensional accuracy and smooth surfaces. The types of metal commonly used in die casting include:
- Aluminum
- Zinc
- Magnesium
- Copper
- Lead
The die casting process is widely utilized in various industries, including automotive, aerospace, electronics, and consumer goods, thanks to its ability to create complex geometries with minimal waste.
The Role of Die Casting Die in the Process
The die casting die is integral to the die casting process. It is a specialized tool designed to shape the molten metal into the desired form. The characteristics of die casting dies include:
- Durability: Made from high-strength materials to withstand repeated use.
- Precision: Designed for accuracy to maintain the exact specifications required for the final product.
- Heat Resistance: Able to endure high temperatures associated with molten metal.
Types of Die Casting Dies
There are two main types of die casting dies:
1. Hot Chamber Die Casting Dies
Hot chamber dies are typically used for metals with low melting points, such as zinc and lead. In this system, the molten metal is kept in a chamber that is heated, allowing for a continuous flow into the mold.
2. Cold Chamber Die Casting Dies
Cold chamber dies are suited for metals with higher melting points, such as aluminum and magnesium. In this process, the molten metal is melted in a separate furnace and then poured into the chamber before being injected into the die. This method helps maintain efficient temperature control and prevents contamination.
Benefits of Using Die Casting
Employing the die casting process offers several advantages that make it popular across various sectors:
- Cost Efficiency: High production rates reduce overall costs.
- Complex Designs: Ability to create intricate shapes that are difficult with other manufacturing methods.
- Excellent Surface Finish: Parts come out of the die requiring minimal post-processing.
- High Strength: Products have superior mechanical properties compared to parts made through other fabrication methods.
Applications of Die Casting
Die casting is utilized in numerous applications, including:
Automotive Industry
In the automotive industry, die casting produces components such as engine blocks, transmission cases, and various parts for electrical systems. The requirement for lightweight and high-strength components makes die casting an ideal choice.
Aerospace Industry
The aerospace sector uses die casting for parts that must endure extreme stress and temperature variations. Components such as brackets, housings, and structural parts are often created using this process.
Consumer Electronics
In electronics, die casting is commonly used for casings and housings for devices, ensuring they are lightweight yet durable.
Best Practices in Die Casting
To achieve optimal results in die casting, it's critical to adhere to best practices throughout the process:
1. Design Optimization
Each casting project should start with an efficient design that considers material flow, cooling, and shrinkage. Collaborating with experienced engineers can ensure that designs are suited for die casting.
2. Material Selection
Choosing the right material for both the die and the casting is crucial. Different metals exhibit varying properties, such as melting points and thermal expansion, significantly impacting the final product.
3. Regular Maintenance of Dies
Regular inspections and maintenance of the die casting die ensure high quality in production and prolong its lifespan, reducing costs for replacements.
4. Invest in Quality Technology
Utilizing advanced machinery and automation can enhance precision and reliability in the die casting process, ultimately leading to a higher quality end product.
Conclusion
In summary, die casting is a pivotal manufacturing technique, and the die casting die serves as a cornerstone of this process. Understanding the function, types, advantages, applications, and best practices associated with die casting can empower businesses to leverage this technology effectively. As industries continue to seek innovative solutions for metal fabrication, die casting remains at the forefront, promoting efficiency, precision, and cost savings.
Further Exploration
For businesses looking to integrate die casting into their manufacturing processes, it’s essential to partner with skilled metal fabricators. Engaging with professionals like DeepMould.net can provide the expertise needed to navigate the complexities of die casting and achieve lasting results.